NewsDetails
A Comprehensive Review of the Technological Iteration Path of Vehicle - Mounted Filter Presse
author:Shuangcheng time:2025-03-21 18:52:25 Click:169
A Comprehensive Review of the Technological Iteration Path of Vehicle - Mounted Filter Presses
1. Early - stage Basic Structure and Function
1.1 Initial Design
In the early days, vehicle - mounted filter presses were simple adaptations of traditional stationary filter presses onto vehicle platforms. The basic structure mainly included a frame, filter plates, and a simple feeding system. The filter plates were often made of common materials like un - reinforced plastic or basic metal alloys, which had limited strength and corrosion resistance.
1.2 Limited Functionality
These early - model vehicle - mounted filter presses were mainly used for basic solid - liquid separation tasks in relatively less - demanding environments. They had a low degree of automation, relying mostly on manual operation for processes such as filter plate opening and closing, and feeding control. Their dewatering efficiency was relatively low, and the quality of the separated filter cakes was not highly consistent.
2. Development of Mobility - related Technologies
2.1 Chassis and Mounting Optimization
As the demand for better mobility grew, improvements were made to the vehicle chassis on which the filter presses were mounted. Lighter yet stronger chassis materials were selected to reduce the overall weight of the vehicle - mounted unit while ensuring sufficient load - bearing capacity. Specialized mounting mechanisms were developed to securely fasten the filter press components to the chassis, minimizing vibrations during transportation and ensuring stable operation at work sites.
2.2 Power and Transmission Systems for Mobility
To meet the power requirements of the filter press during mobile operation, more efficient power and transmission systems were introduced. Hybrid power systems, combining internal combustion engines and electric motors, became popular. The internal combustion engine could be used for long - distance transportation, while the electric motor provided the precise and stable power needed for the filter press operation at the work site. This not only improved fuel efficiency but also reduced emissions during operation.
3. Enhancement of Filtration and Dewatering Technologies
3.1 Advanced Filter Plate Materials and Designs
Filter plate materials evolved from basic plastics and metals to high - performance polymers like reinforced polypropylene. These new materials offered better corrosion resistance, higher strength, and improved thermal stability. In terms of design, filter plates with optimized surface patterns and internal channels were developed. For example, filter plates with concave - convex surfaces increased the effective filtration area, and the internal channels were designed to facilitate the even distribution of slurry and the smooth discharge of filtrate, significantly improving filtration efficiency.
3.2 Sophisticated Dewatering Techniques
The development of advanced dewatering techniques such as diaphragm pressing technology was a major leap. Diaphragm filter plates were introduced, which could perform secondary pressing on the filter cake after the initial filtration. By injecting high - pressure fluids (such as water or compressed air) into the diaphragm, the filter cake was further compressed, reducing its moisture content substantially. Additionally, multi - stage dewatering processes were integrated, where different dewatering methods were applied in sequence to achieve better results.
4. Introduction of Automation and Control Systems
4.1 PLC - based Control
With the progress of electronics and control technology, Programmable Logic Controllers (PLCs) were adopted in vehicle - mounted filter presses. PLCs enabled the automation of various operations, including filter plate opening and closing, feeding control, and pressing process management. Sensors were installed to monitor key parameters such as pressure, flow rate, and temperature in real - time. The PLC system could adjust the operation of the filter press according to the sensor - collected data, ensuring optimal performance and consistency in the dewatering process.
4.2 Remote Monitoring and Control
In recent years, the development of wireless communication technology has led to the implementation of remote monitoring and control systems. Vehicle - mounted filter presses can now be connected to a central control station via wireless networks. Operators can remotely monitor the running status of the filter press, receive real - time alarms in case of malfunctions, and even adjust operation parameters from a distance. This not only improves operational efficiency but also reduces the need for on - site personnel, especially in hazardous or hard - to - reach work environments.
5. Integration with Environmental and Industry - specific Requirements
5.1 Environmental - friendly Design
In response to increasing environmental awareness, vehicle - mounted filter presses have been designed with more environmental - friendly features. Energy - saving technologies were incorporated, such as variable - frequency drives for motors to reduce power consumption. Closed - loop systems were developed to minimize the discharge of pollutants, especially in applications where the filtered liquid may contain harmful substances. For example, in wastewater treatment, the filtrate was recycled and reused within the system as much as possible.
5.2 Industry - specific Customization
Vehicle - mounted filter presses are now highly customized according to different industry needs. In the mining industry, filter presses are designed to handle large volumes of slurry with high solid - content and abrasive particles. Special wear - resistant materials are used for key components, and the filtration capacity is optimized to meet the high - volume processing requirements. In the food and beverage industry, filter presses are designed to meet strict hygiene standards, with materials that are non - toxic and easy to clean, and the filtration process is carefully controlled to ensure product quality.
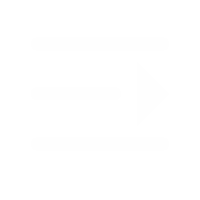
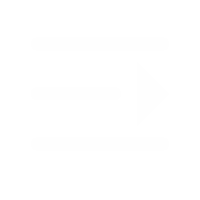
—— Contact:Manager
—— Tel:+86 16632826789
—— Email:sales@hbscfilterpress.com
—— Url:http://www.hbscfilterpress.com
—— Address:West Zone of Economic Development Zone, Fucheng County, Hengshui City, Hebei Province