NewsDetails
Vehicle - Mounted Filter Press Maintenance Guide
author:Shuangcheng time:2025-03-21 18:58:04 Click:186
Visual Inspection: Routinely check filter plates for any signs of cracks, deformation, or wear. Cracks can lead to leakage during the filtration process, reducing the efficiency of the filter press. Use a flashlight to carefully examine the surface and edges of each plate. If a crack is detected, replace the filter plate immediately.
Alignment Check: Ensure that the filter plates are properly aligned within the frame. Misaligned plates can cause uneven pressure distribution, resulting in poor filtration and potential damage to the plates. Check the positioning of the plates regularly and adjust as necessary.
1.2 Moving Parts (Pumps, Motors, and Chains)
Pump Inspection: Inspect the feeding pump and hydraulic pump for leaks, abnormal noises, or vibrations. Leaks can indicate worn - out seals or damaged pump components. Check the pump's oil level and change the oil according to the manufacturer's recommendations. For centrifugal pumps, examine the impeller for signs of wear or clogging, which can affect the flow rate and pressure.
Motor Maintenance: Check the motor's electrical connections for tightness and signs of corrosion. Clean the motor's cooling fins regularly to prevent overheating. Monitor the motor's operating temperature and current draw. If the temperature is too high or the current draw exceeds the rated value, there may be an issue with the motor, such as a bearing problem or electrical fault.
Chain and Sprocket Lubrication: For filter presses with chain - driven components, such as the plate - pulling mechanism, regularly lubricate the chains and sprockets. Use a high - quality chain lubricant to reduce friction and wear. Check the chain tension and adjust it if necessary. A loose chain can cause skipping or misalignment, while an overly tight chain can put excessive stress on the components.
2. Hydraulic System Maintenance
2.1 Fluid Level and Quality
Level Check: Regularly check the hydraulic fluid level in the reservoir. The fluid level should be within the marked range on the sight glass. If the level is low, add the recommended hydraulic fluid. Avoid overfilling, as this can cause pressure problems and fluid leakage.
Quality Inspection: Periodically sample the hydraulic fluid to check for contamination. Contaminated fluid can cause damage to hydraulic components, such as valves and cylinders. Look for signs of discoloration, cloudiness, or the presence of particles. If the fluid is contaminated, replace it with clean, fresh hydraulic fluid.
2.2 Hydraulic Valves and Cylinders
Valve Functionality: Test the hydraulic valves to ensure they are operating correctly. Check for proper opening and closing, and make sure there are no leaks. If a valve is not functioning properly, it may need to be cleaned, repaired, or replaced. Some valves can be adjusted to optimize the hydraulic system's performance.
Cylinder Seal Inspection: Examine the seals on hydraulic cylinders for signs of wear or leakage. Leaking cylinder seals can result in a loss of hydraulic pressure and affect the operation of the filter press. Replace worn - out seals promptly to maintain the integrity of the hydraulic system.
3. Filtration Medium Maintenance
3.1 Filter Cloth Cleaning and Replacement
Cleaning: After each filtration cycle, clean the filter cloth to remove any residual solids. Use a high - pressure water jet or a suitable cleaning agent, depending on the type of filter cloth and the nature of the filtered material. For some filter cloths, chemical cleaning may be required to remove stubborn deposits. However, be careful not to damage the filter cloth during the cleaning process.
Replacement: Regularly inspect the filter cloth for signs of wear, holes, or reduced filtration efficiency. If the filter cloth is damaged or no longer effectively separating solids from the liquid, replace it with a new one. Choose a filter cloth with the appropriate pore size and material properties based on the filtration requirements.
3.2 Filter Membrane (if applicable)
Inspection: For filter presses with filter membranes, such as in some advanced filtration applications, carefully inspect the membranes for any signs of damage, cracks, or fouling. Membrane fouling can significantly reduce the filtration performance. Use a gentle cleaning method recommended by the manufacturer to remove deposits on the membrane surface.
Maintenance Schedule: Follow the manufacturer's recommended maintenance schedule for the filter membrane. This may include periodic chemical cleaning, back - flushing, or membrane replacement at specific intervals to ensure optimal filtration performance.
4. Electrical System Maintenance
4.1 Wiring and Connections
Visual Inspection: Regularly inspect the electrical wiring for signs of fraying, cracking, or loose connections. Damaged wiring can pose a safety hazard and cause electrical malfunctions. Tighten any loose connections and replace any damaged wires immediately.
Grounding Check: Ensure that the electrical system of the filter press is properly grounded. A good ground connection protects against electrical shocks and helps prevent equipment damage due to electrical surges. Check the grounding wires and connections regularly.
4.2 Control Panel and Sensors
Panel Functionality: Test the control panel to ensure that all the switches, buttons, and indicators are working correctly. Check the display for any error messages or abnormal readings. If there are issues with the control panel, it may be necessary to repair or replace the faulty components.
Sensor Calibration: Calibrate the sensors, such as pressure sensors and level sensors, regularly. Incorrectly calibrated sensors can lead to inaccurate control of the filter press operation. Follow the manufacturer's instructions for sensor calibration to ensure reliable performance.
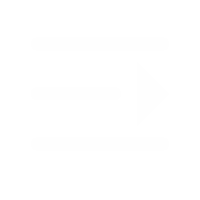
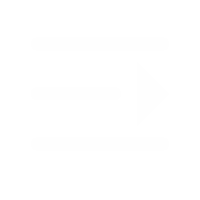
—— Contact:Manager
—— Tel:+86 16632826789
—— Email:sales@hbscfilterpress.com
—— Url:http://www.hbscfilterpress.com
—— Address:West Zone of Economic Development Zone, Fucheng County, Hengshui City, Hebei Province