NewsDetails
Design Key Points of the Explosion - Proof System for Hydraulic Chamber Filter Press
author:Shuangcheng time:2025-03-21 23:24:26 Click:100
1. Introduction
In certain industrial environments, such as the petrochemical, coal - mining, and pharmaceutical industries, where there are potentially explosive gas - air mixtures or combustible dust - air mixtures, the use of hydraulic chamber filter presses requires the implementation of reliable explosion - proof systems. This article elaborates on the key design points of the explosion - proof system for hydraulic chamber filter presses to ensure safe operation in hazardous areas.
2. Hazardous Area Classification
2.1 Gas - Hazardous Areas
Zone 0: An area in which an explosive gas - air mixture is present continuously or for long periods. In a petrochemical plant, for example, the interior of a storage tank containing flammable liquids with a high vapor pressure may be classified as Zone 0.
Zone 1: An area in which an explosive gas - air mixture is likely to occur in normal operation. This could include areas around open flanges or valves where flammable gas may be released during routine maintenance or process operations.
Zone 2: An area in which an explosive gas - air mixture is not likely to occur in normal operation and, if it does occur, will exist only for a short period. For instance, the outer area of a well - ventilated pump house handling flammable liquids may be Zone 2.
2.2 Dust - Hazardous Areas
Zone 20: An area in which combustible dust - air mixtures are present continuously, frequently, or for long periods. In a coal - processing plant, the interior of a dust - collection hopper where coal dust is constantly accumulating may be Zone 20.
Zone 21: An area in which combustible dust - air mixtures are likely to occur during normal operation. This might be the area around a conveyor belt in a flour mill where flour dust is regularly generated during the conveying process.
Zone 22: An area in which combustible dust - air mixtures are not likely to occur in normal operation and, if they do occur, will exist only for a short period. An example could be the outer area of a packaging area for powdered chemicals with proper dust - control measures.
Accurate hazardous area classification is crucial as it determines the type and level of explosion - proof protection required for the hydraulic chamber filter press and its associated components.
3. Explosion - Proof Principles
3.1 Flameproof Enclosure (Ex d)
Design Concept: The equipment is enclosed in a strong enclosure that can withstand an internal explosion of an explosive gas - air mixture without allowing the flame or hot gases to escape and ignite the surrounding explosive atmosphere. The enclosure is designed with specific joints and gaps to quench the flame.
Application in Filter Press: For components such as motors, control panels, and hydraulic pumps that may generate sparks or high temperatures during operation, they can be housed in flameproof enclosures. The enclosure material, such as cast iron or steel, should have sufficient strength to withstand the internal explosion pressure. The joints between different parts of the enclosure are carefully designed and manufactured to ensure that the maximum allowable gap is maintained. For example, the flanged joints of the enclosure should have a certain width and surface roughness to ensure proper flame quenching.
3.2 Intrinsic Safety (Ex i)
Design Concept: Intrinsic safety limits the energy available in an electrical circuit to a level that is incapable of igniting an explosive gas - air or combustible dust - air mixture. This is achieved by using special components and circuit design techniques to limit the voltage, current, and stored energy in the circuit.
Application in Filter Press: Sensors, control circuits, and communication lines that are used in the operation of the filter press can be designed to be intrinsically safe. For example, intrinsically safe pressure sensors can be used to monitor the pressure in the hydraulic system. These sensors are designed with low - power components and appropriate protection circuits to ensure that any electrical sparks or heat generated during normal operation or in the event of a fault are below the ignition energy of the surrounding explosive mixture.
3.3 Pressurized Enclosure (Ex p)
Design Concept: The enclosure of the equipment is pressurized with clean air or an inert gas, such as nitrogen. This positive pressure prevents the entry of explosive gas - air or combustible dust - air mixtures into the enclosure.
Application in Filter Press: Larger components or areas of the filter press, such as the control room or the main body of the filter press where multiple electrical and mechanical components are located, can be designed as pressurized enclosures. A reliable pressure - monitoring system is installed to ensure that the pressure inside the enclosure is always above the atmospheric pressure by a certain margin. In case the pressure drops below the set value, an alarm is triggered, and measures are taken to restore the pressure, such as opening additional air or inert - gas supply valves.
4. Component - Level Design Considerations
4.1 Electrical Components
Explosion - Proof Motors: Motors used in the hydraulic chamber filter press, such as those for driving the hydraulic pump or the conveyor for discharging the filter cake, must be explosion - proof. They should be selected according to the hazardous area classification. For Zone 1 and Zone 2 gas - hazardous areas, motors with flameproof enclosures (Ex d) are commonly used. In dust - hazardous areas, motors with appropriate dust - ignition - proof enclosures are required. The motor's power rating should be sufficient to meet the operational requirements of the filter press, and its cooling system should be designed to ensure proper heat dissipation even in the presence of the potentially explosive atmosphere.
Control Panels: Control panels house various electrical control components, such as switches, relays, and programmable logic controllers (PLCs). They should be designed as explosion - proof enclosures, following the relevant explosion - proof standards. Intrinsic - safety - type control circuits can be incorporated into the control panels to ensure safe operation. The wiring in the control panels should be carefully routed and protected to prevent electrical faults that could potentially cause ignition.
Sensors: Pressure sensors, level sensors, and temperature sensors used in the filter press operation need to be explosion - proof. Intrinsic - safety - type sensors are often preferred as they can be safely installed in hazardous areas. These sensors should be calibrated regularly to ensure accurate measurement and reliable operation.
4.2 Hydraulic System Components
Hydraulic Pump: The hydraulic pump, which is a key component of the hydraulic system, should be designed to operate safely in hazardous areas. If the pump is driven by an electric motor, the motor must be explosion - proof as mentioned above. The pump body should be made of materials that are resistant to corrosion and capable of withstanding the operating pressure. Seals and gaskets in the pump should be carefully selected to prevent leakage of hydraulic fluid, as any leakage could potentially create a fire or explosion hazard in the presence of an explosive atmosphere.
Hydraulic Hoses and Pipes: Hydraulic hoses and pipes should be made of materials that are resistant to abrasion, pressure, and chemical corrosion. In hazardous areas, they should also be designed to prevent the release of hydraulic fluid in case of damage. Special explosion - proof hoses with additional layers of protection or metal - braided hoses can be used. The connections between hoses and pipes should be secure and leak - proof, and regular inspections should be carried out to detect any signs of wear or damage.
4.3 Mechanical Components
Filter Plates and Frames: The filter plates and frames of the filter press should be made of materials that are not prone to generating sparks during normal operation or in case of mechanical impact. Non - sparking materials, such as certain types of stainless steel or non - metallic composites, can be used. The mechanical movement of the filter plates, such as during the opening and closing process, should be smooth and free from any abnormal friction or impact that could potentially generate heat or sparks.
Conveyor Systems: Conveyor systems used for discharging the filter cake should be designed to operate safely in hazardous areas. The conveyor belts should be made of non - combustible materials, and the drive motors and rollers should be explosion - proof. Regular maintenance and cleaning of the conveyor system are necessary to prevent the accumulation of combustible dust or residues.
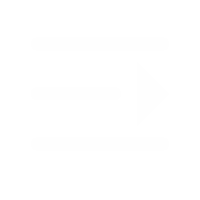
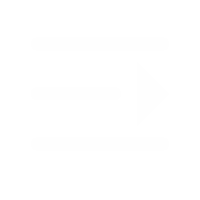
—— Contact:Manager
—— Tel:+86 16632826789
—— Email:sales@hbscfilterpress.com
—— Url:http://www.hbscfilterpress.com
—— Address:West Zone of Economic Development Zone, Fucheng County, Hengshui City, Hebei Province