NewsDetails
Optimization Scheme for the Lubrication System of Hydraulic Chamber Filter Press
author:Shuangcheng time:2025-03-21 23:25:44 Click:126
The lubrication system of a hydraulic chamber filter press plays a crucial role in ensuring the smooth operation of its mechanical components, reducing friction, minimizing wear, and extending the service life of the equipment. An optimized lubrication system can enhance the overall performance, reliability, and energy efficiency of the filter press. This article presents a comprehensive optimization scheme for the lubrication system of a hydraulic chamber filter press.
2. Current Issues in the Lubrication System
2.1 Inadequate Lubricant Supply
Uneven Distribution: In some filter presses, the existing lubrication system may not distribute lubricant evenly to all moving parts. For example, in a multi - plate filter press, certain hinge points or sliding surfaces may receive less lubricant than others, leading to accelerated wear in those areas.
Insufficient Quantity: The amount of lubricant supplied may be insufficient, especially during continuous high - load operation. This can cause increased friction between components, generating more heat and potentially leading to component failure.
2.2 Lubricant Contamination
Solid Particle Ingress: In industrial environments, dust, dirt, and small metal particles can enter the lubrication system. In a mining - related filter press operation, for instance, fine ore particles can infiltrate the lubricant through openings in seals or during maintenance procedures. These solid particles can act as abrasives, increasing wear and reducing the effectiveness of the lubricant.
Moisture Contamination: Moisture can enter the lubrication system, either from the surrounding atmosphere or through leaks in hydraulic components. In wastewater treatment plants, where the filter press is exposed to a humid environment, moisture can mix with the lubricant, causing corrosion of metal parts and emulsification of the lubricant, which deteriorates its lubricating properties.
2.3 Inefficient Lubrication Methods
Manual Lubrication: Some filter presses still rely on manual lubrication, which is time - consuming and inconsistent. Operators may not be able to lubricate all components at the right intervals, and the amount of lubricant applied may vary significantly. This lack of precision in manual lubrication can lead to over - lubrication in some areas (wasting lubricant and attracting more dirt) and under - lubrication in others.
Single - Point Lubrication: Using a single - point lubrication system for multiple components may not be sufficient to meet the specific lubrication requirements of each part. Different moving parts in a filter press, such as hydraulic cylinders, chains, and bearings, have varying speeds, loads, and operating temperatures, and thus require different lubrication strategies.
3. Optimization Measures
3.1 Lubricant Selection and Management
Proper Lubricant Grade: Select a lubricant that is suitable for the specific operating conditions of the filter press. Consider factors such as the type of mechanical components (e.g., whether they are bearings, gears, or hydraulic cylinders), the operating temperature range, the load applied, and the presence of contaminants in the environment. For high - temperature applications, a synthetic lubricant with high thermal stability can be chosen. In a dusty environment, a lubricant with good anti - wear and dirt - suspending properties is preferred.
Lubricant Filtration and Purification: Install a high - efficiency filtration system in the lubrication circuit to remove solid particles and moisture. A multi - stage filter can be used, with an initial coarse - filter to remove large particles and a fine - filter to capture smaller contaminants. Additionally, consider using a moisture separator to remove any water present in the lubricant. Regularly monitor the condition of the lubricant using techniques such as oil analysis to determine when it needs to be replaced or further purified.
3.2 Improvement of Lubrication Distribution
Multi - Point Automatic Lubrication System: Replace the existing inefficient lubrication methods with a multi - point automatic lubrication system. This system can be programmed to supply the right amount of lubricant to each critical moving part at pre - set intervals. For example, it can be configured to lubricate the hinge points of filter plates, the piston rods of hydraulic cylinders, and the bearings of conveyor systems independently. The automatic system ensures consistent and accurate lubrication, reducing the risk of under - or over - lubrication.
Lubrication Line Design: Optimize the design of the lubrication lines to ensure even distribution of lubricant. Use proper 管径 s to maintain the required flow rate and pressure. Install flow - control valves at key points in the lubrication lines to regulate the amount of lubricant reaching each component. Ensure that the lubrication lines are properly routed to avoid kinks or blockages that could disrupt the lubricant flow.
3.3 Sealing and Protection
Enhanced Sealing Devices: Upgrade the sealing devices around moving parts to prevent the ingress of contaminants into the lubrication system. For example, use high - quality lip seals or mechanical seals on hydraulic cylinders and bearings. These seals should be selected based on the operating conditions, such as pressure, temperature, and speed. Regularly inspect and replace seals that show signs of wear or damage to maintain their effectiveness.
Protective Covers and Shields: Install protective covers and shields over exposed moving parts to reduce the amount of dust, dirt, and moisture that can reach the lubrication system. For chain - driven components, enclose them in protective casings. These covers not only protect the lubrication system but also enhance the safety of the filter press operation.
3.4 Monitoring and Maintenance
Condition Monitoring Sensors: Install sensors to monitor the condition of the lubrication system, such as temperature sensors to detect abnormal heating due to poor lubrication, pressure sensors to ensure proper lubricant flow, and vibration sensors to identify any excessive vibrations caused by worn - out or under - lubricated components. Connect these sensors to a central monitoring system that can alert operators in case of any issues.
Regular Maintenance Schedule: Develop a detailed regular maintenance schedule for the lubrication system. This includes tasks such as checking the lubricant level, inspecting the filters, replacing worn - out seals, and calibrating the automatic lubrication system. Train maintenance personnel to perform these tasks accurately and efficiently.
4. Expected Benefits of the Optimization
4.1 Extended Component Life
By ensuring proper lubrication and reducing friction, the wear rate of mechanical components such as bearings, gears, and hydraulic cylinders will be significantly reduced. This can lead to a substantial extension of their service life, reducing the frequency of component replacements and associated downtime.
4.2 Improved Energy Efficiency
Reduced friction due to optimized lubrication means that the filter press requires less energy to operate. This can result in lower electricity consumption, leading to cost savings over time.
4.3 Enhanced Reliability
A well - optimized lubrication system with effective monitoring and maintenance measures can minimize the risk of unexpected breakdowns. The filter press will operate more smoothly and consistently, improving the overall reliability of the industrial process in which it is used.
4.4 Cost Savings
The combination of extended component life, reduced energy consumption, and improved reliability leads to overall cost savings. Fewer component replacements, lower energy bills, and less downtime translate into a more cost - effective operation of the hydraulic chamber filter press.
5. Conclusion
The optimization of the lubrication system of a hydraulic chamber filter press is essential for improving its performance, reliability, and cost - effectiveness. By addressing the current issues in the lubrication system, implementing appropriate optimization measures, and reaping the expected benefits, the filter press can operate more efficiently and with fewer maintenance problems in various industrial applications. Regular monitoring and continuous improvement of the lubrication system are also crucial to ensure its long - term effectiveness.
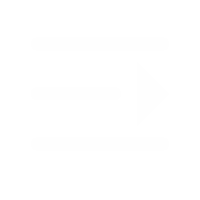
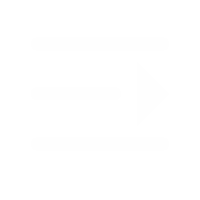
—— Contact:Manager
—— Tel:+86 16632826789
—— Email:sales@hbscfilterpress.com
—— Url:http://www.hbscfilterpress.com
—— Address:West Zone of Economic Development Zone, Fucheng County, Hengshui City, Hebei Province