NewsDetails
In - depth Troubleshooting of Filter Press Operation Problems
author:Shuangcheng time:2025-03-21 23:36:38 Click:60
1. Introduction
Filter presses are crucial equipment in industries such as mining, wastewater treatment, and chemical engineering for solid - liquid separation. When they encounter operational issues, it is essential to conduct an in - depth investigation to identify the root causes and implement effective solutions. This article focuses on the systematic approach to troubleshooting common problems in filter press operation.
2. General Troubleshooting Steps
2.1 Problem Identification
Observation: The first step is to carefully observe the symptoms of the problem. This includes noting any abnormal noises, vibrations, leaks, or changes in the performance of the filter press, such as reduced filtration efficiency or poor filter cake quality. For example, if there is a hissing sound during operation, it may indicate a leak in the hydraulic system or a problem with the pressure - relief valve.
Data Collection: Gather relevant data about the filter press operation, such as the pressure readings, flow rates of the slurry and filtrate, and the temperature of the hydraulic oil. Comparing these data with the normal operating parameters can help in pinpointing the source of the problem. Unusually high pressure during filtration might suggest a blockage in the filter medium or an issue with the feed system.
2.2 Equipment Inspection
Visual Inspection: Conduct a comprehensive visual inspection of the entire filter press. Check the filter plates for cracks, warping, or damage. Inspect the filter cloth for tears, holes, or signs of clogging. Examine the hydraulic hoses, pipes, and fittings for leaks or loose connections. In a multi - plate filter press, misaligned filter plates can cause uneven pressure distribution and lead to operational problems.
Mechanical Component Check: Examine the moving parts of the filter press, such as the plate - moving mechanism, hinges, and conveyor belts (if applicable). Ensure that they are properly lubricated and not experiencing excessive wear or binding. A worn - out bearing in the plate - moving mechanism can cause erratic movement of the filter plates.
Hydraulic System Inspection: Check the hydraulic oil level and its condition. Low oil levels can cause cavitation in the hydraulic pump, while contaminated oil can damage the hydraulic components. Inspect the hydraulic pump, valves, and cylinders for leaks, abnormal noises, or signs of malfunction. Test the functionality of the pressure gauge and other control devices to ensure accurate readings and proper operation.
2.3 Process - related Analysis
Slurry Characteristics: Consider the properties of the slurry being processed. Changes in the solid - content, particle size distribution, viscosity, or chemical composition of the slurry can impact the performance of the filter press. For example, if the solid - content of the slurry suddenly increases, it may overload the filter press and lead to reduced filtration efficiency.
Operating Parameters: Review the operating parameters of the filter press, such as the feed rate, pressure, and filtration time. Incorrect settings of these parameters can cause various problems. A too - high feed rate may result in uneven distribution of the slurry in the filter chamber, leading to poor filter cake formation.
3. Troubleshooting Specific Problems
3.1 Low Filtration Efficiency
Possible Causes:
Clogged Filter Cloth: Fine solid particles in the slurry can accumulate in the pores of the filter cloth over time, reducing its permeability. This can be due to improper pre - treatment of the slurry or extended use of the filter cloth without cleaning.
Inadequate Pressure: If the hydraulic system fails to generate sufficient pressure, the slurry may not be effectively filtered. This could be caused by a malfunctioning hydraulic pump, a leak in the hydraulic system, or incorrect pressure settings.
Improper Feed Rate: A feed rate that is either too high or too low can affect filtration efficiency. A high feed rate may cause the slurry to bypass the filter medium, while a low feed rate may result in incomplete filling of the filter chamber.
Solutions:
Clean or Replace Filter Cloth: If the filter cloth is clogged, clean it using a high - pressure water jet or a suitable cleaning agent. If the clogging is severe or the filter cloth is damaged, replace it with a new one.
Check and Adjust Pressure: Inspect the hydraulic system for leaks, malfunctions in the pump or valves, and ensure that the pressure settings are correct. Repair or replace any faulty components and adjust the pressure to the appropriate level.
Optimize Feed Rate: Adjust the feed rate according to the characteristics of the slurry and the capacity of the filter press. Monitor the filtration process to find the optimal feed rate that maximizes filtration efficiency.
3.2 Filter Cake Quality Issues
Possible Causes:
Uneven Pressure Distribution: Uneven pressure on the filter plates can lead to uneven filter cake formation. This can be caused by misaligned filter plates, worn - out gaskets between the plates, or a problem with the hydraulic system that results in non - uniform pressure application.
Incorrect Slurry Properties: Changes in the slurry properties, such as an inconsistent solid - content or particle size distribution, can affect the quality of the filter cake. For example, if the particle size is too fine, it may be difficult to form a dense and stable filter cake.
Short Filtration Time: If the filtration time is too short, the filter cake may not have sufficient time to form properly, resulting in a wet and crumbly cake.
Solutions:
Align Filter Plates and Replace Gaskets: Check and align the filter plates to ensure even pressure distribution. Replace any worn - out gaskets between the plates to improve the seal.
Adjust Slurry Properties: If possible, adjust the slurry properties to ensure consistency. This may involve pre - treatment processes such as dilution, coagulation, or flocculation to improve the filterability of the slurry.
Optimize Filtration Time: Increase the filtration time to allow the filter cake to form properly. Monitor the filter cake quality and adjust the filtration time as needed.
3.3 Leakage Problems
Possible Causes:
Worn - out Gaskets: The gaskets between the filter plates are responsible for sealing the filter chamber. Over time, they can wear out due to continuous pressure and friction, resulting in leaks.
Damaged Filter Plates or Filter Cloth: Cracks or holes in the filter plates or filter cloth can also cause leakage. Physical damage to these components can occur during operation, such as due to impact or excessive pressure.
Loose Connections in the Hydraulic System: Loose fittings or connections in the hydraulic hoses, pipes, or valves can lead to hydraulic fluid leakage.
Solutions:
Replace Gaskets: Identify the worn - out gaskets and replace them with new ones. Ensure that the new gaskets are of the correct size and material for the filter press.
Repair or Replace Damaged Components: If the filter plates or filter cloth are damaged, repair or replace them as appropriate. For minor damage to the filter cloth, patching may be possible, but for significant damage, replacement is usually necessary.
Tighten Connections in the Hydraulic System: Check all the connections in the hydraulic system and tighten any loose fittings. Inspect the hoses and pipes for signs of damage and replace them if necessary.
4. Preventive Measures
Regular Maintenance: Establish a regular maintenance schedule for the filter press. This includes tasks such as lubricating moving parts, checking the hydraulic system, cleaning the filter cloth, and inspecting the filter plates. Regular maintenance can help detect and address potential problems before they develop into major issues.
Operator Training: Provide comprehensive training to the operators of the filter press. They should be familiar with the proper operation procedures, the normal operating parameters of the equipment, and how to identify and respond to early signs of problems. Well - trained operators can help prevent many operational problems through proper handling of the filter press.
Monitoring and Data Analysis: Continuously monitor the operation of the filter press using sensors and data - logging systems. Analyze the collected data regularly to detect trends and anomalies. This can help in predicting potential problems and taking preventive actions in a timely manner.
5. Conclusion
Troubleshooting filter press operation problems requires a systematic approach that involves problem identification, equipment inspection, and process - related analysis. By addressing specific problems such as low filtration efficiency, filter cake quality issues, and leakage, and implementing preventive measures, the performance and reliability of the filter press can be maintained, ensuring smooth operation in industrial processes.
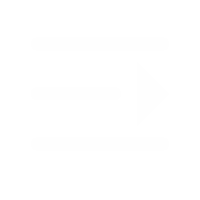
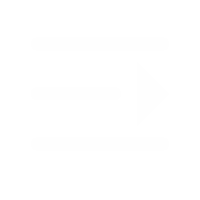
—— Contact:Manager
—— Tel:+86 16632826789
—— Email:sales@hbscfilterpress.com
—— Url:http://www.hbscfilterpress.com
—— Address:West Zone of Economic Development Zone, Fucheng County, Hengshui City, Hebei Province