NewsDetails
Strategies for Preventing Filter Cloth Clogging in Diaphragm Filter Presses
author:Shuangcheng time:2025-03-21 23:52:47 Click:153
1. Pretreatment of Slurry
1.1 Solid - Liquid Separation and Particle Size Adjustment
Screening and Sedimentation: Before feeding the slurry into the diaphragm filter press, pass it through screens or sedimentation tanks. Screens with appropriate mesh sizes can remove large - sized solid particles that could potentially cause blockages in the filter cloth. For example, in a mining - related slurry, a vibrating screen can be used to separate out rocks and large aggregates. Sedimentation tanks allow heavier particles to settle at the bottom over time. This pretreatment reduces the load on the filter cloth and minimizes the risk of large - particle - induced clogging.
Flocculation and Coagulation: Add flocculants or coagulants to the slurry. These chemicals cause fine solid particles to agglomerate into larger flocs. In wastewater treatment plants, for instance, aluminum sulfate or polyacrylamide can be added to the sludge slurry. The larger flocs are easier to filter and are less likely to penetrate and clog the pores of the filter cloth.
1.2 pH Adjustment
Optimizing Chemical Reactivity: Adjust the pH of the slurry to a range that minimizes the solubility of certain substances. In some industrial processes, metal ions in the slurry can precipitate out and clog the filter cloth at specific pH values. By controlling the pH, these precipitation reactions can be either enhanced (if the precipitates are easy to filter) or inhibited. For example, in a chemical manufacturing process where metal hydroxide precipitates are formed, adjusting the pH to the optimal range for floc formation can improve filtration efficiency and prevent filter cloth clogging.
2. Filter Cloth Selection and Installation
2.1 Choosing the Right Filter Cloth Material
Chemical Compatibility: Select a filter cloth material that is chemically compatible with the slurry. In acidic environments, materials like polyester or polypropylene filter cloths are often suitable as they have good acid resistance. In alkaline or high - temperature applications, nylon - based filter cloths may be more appropriate. For example, in a pharmaceutical filtration process involving acidic solutions, a polyester filter cloth with a tight weave can effectively separate solids while resisting chemical degradation, reducing the chance of cloth damage and subsequent clogging.
Pore Size and Structure: Match the pore size of the filter cloth to the particle size distribution of the slurry. If the pores are too large, fine particles will pass through and may accumulate in the deeper layers of the filter cloth, leading to clogging. Conversely, if the pores are too small, the filtration rate will be severely reduced. A multi - layer filter cloth with a graded pore structure, where the outer layer has larger pores for initial coarse filtration and the inner layers have smaller pores for finer separation, can be an effective choice for slurries with a wide range of particle sizes.
2.2 Proper Installation
Tight and Even Fit: Ensure that the filter cloth is installed tightly and evenly on the filter plates. Loose or wrinkled filter cloth can cause uneven filtration, with some areas receiving more slurry than others. This can lead to local clogging as the excess slurry in certain areas overwhelms the filter cloth's capacity. Use appropriate fastening methods, such as clips or ropes, to secure the filter cloth firmly in place.
Sealing Integrity: Check and maintain the sealing between the filter cloth and the filter plates. Any gaps or leaks in the seal can allow slurry to bypass the filtration area and cause deposits on the filter cloth edges, which can spread and contribute to overall clogging. Use sealants or gaskets as recommended by the filter press manufacturer to ensure a tight seal.
3. Operating Parameter Optimization
3.1 Feeding Rate and Pressure Control
Steady Feeding: Maintain a stable feeding rate of the slurry into the filter press. Sudden increases in the feeding rate can overload the filter cloth, forcing more particles into the pores and increasing the likelihood of clogging. Use variable - speed pumps or flow - control valves to regulate the feeding rate. For example, in a continuous - operation diaphragm filter press, a programmable logic controller (PLC) can be used to adjust the pump speed based on the pressure in the filter chamber and the filtration rate.
Appropriate Pressure: Set the feeding pressure within the recommended range. Excessive pressure can push particles through the filter cloth more forcefully, increasing the chance of pore blockage. On the other hand, too low a pressure may result in incomplete filtration and the formation of a loose filter cake, which can also cause problems. Monitor the pressure during the filtration process and make adjustments as necessary.
3.2 Filtration Time Management
Optimal Filtration Duration: Determine the appropriate filtration time based on the characteristics of the slurry and the desired filter cake quality. Prolonged filtration times can lead to the accumulation of more solids on the filter cloth, increasing the risk of clogging. However, if the filtration time is too short, the filter cake may not form properly, and fine particles may pass through. Conduct pilot tests or use historical data to establish the optimal filtration time for different types of slurries.
4. Cleaning and Maintenance
4.1 Regular Back - flushing
Scheduled Back - flushing Cycles: Implement a regular back - flushing schedule for the filter cloth. Back - flushing involves reversing the flow of a cleaning fluid (usually water or a suitable solvent) through the filter cloth to dislodge the accumulated solids. The frequency of back - flushing depends on the nature of the slurry and the operating conditions. For a filter press used in a high - volume, continuous - operation industrial process, back - flushing may be required every few hours.
Back - flushing Pressure and Flow Rate: Adjust the pressure and flow rate of the back - flushing fluid to ensure effective cleaning without damaging the filter cloth. The pressure should be sufficient to remove the clogged particles but not so high as to cause mechanical damage to the filter cloth. The flow rate should be optimized to evenly distribute the cleaning fluid across the entire filter cloth surface.
4.2 Periodic Chemical Cleaning
Selecting the Right Cleaning Agents: Use chemical cleaning agents when regular back - flushing is not sufficient to remove stubborn deposits. The choice of cleaning agent depends on the nature of the clogging substances. For example, if the filter cloth is clogged with organic matter, a biodegradable detergent or an enzyme - based cleaner may be effective. In cases of inorganic deposits, such as metal oxides, an acidic or alkaline cleaning solution may be required.
Proper Cleaning Procedure: Follow a proper chemical - cleaning procedure. This typically involves soaking the filter cloth in the cleaning solution for a specified period, followed by thorough rinsing with clean water. Ensure that all traces of the cleaning agent are removed to prevent any adverse effects on subsequent filtration processes.
4.3 Inspection and Replacement
Regular Inspection: Regularly inspect the filter cloth for signs of wear, damage, or clogging. Look for areas where the filter cloth has become discolored, hardened, or has visible holes. Use visual inspection, as well as techniques like air permeability testing, to assess the condition of the filter cloth.
Timely Replacement: Replace the filter cloth when it shows significant signs of clogging or damage that cannot be effectively remedied through cleaning. Timely replacement ensures that the filtration efficiency and quality are maintained, and it also helps prevent more serious problems, such as damage to the filter press components due to increased pressure drop caused by a severely clogged filter cloth.
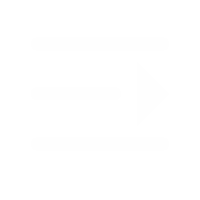
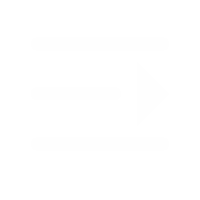
—— Contact:Manager
—— Tel:+86 16632826789
—— Email:sales@hbscfilterpress.com
—— Url:http://www.hbscfilterpress.com
—— Address:West Zone of Economic Development Zone, Fucheng County, Hengshui City, Hebei Province