NewsDetails
How to optimize the operating parameters of diaphragm filter press?
author:Shuangcheng time:2025-03-31 23:53:43 Click:190
Here are some methods for optimizing the operating parameters of diaphragm filter presses:
1. Feed Rate
Control the feeding speed: The feed rate should be stable and within the range recommended by the equipment manufacturer. A constant feed rate ensures uniform filtration and prevents over - loading the filter cloth and filter chamber. For example, in a mineral processing plant, the feed rate of the slurry to the diaphragm filter press is usually controlled at 2 - 3 cubic meters per hour to avoid sudden changes in pressure and filtration efficiency.
Adjust according to the nature of the slurry: If the slurry has a high solid content or a large particle size, the feed rate should be appropriately reduced to prevent clogging of the filter cloth and ensure the quality of the filter cake. Conversely, for slurries with a low solid content and fine particles, the feed rate can be increased within a reasonable range to improve production efficiency.
2. Feed Pressure
Set the appropriate pressure value: The feed pressure is a crucial parameter affecting the filtration effect. Generally, the feed pressure of diaphragm filter presses is between 0.4 and 0.8 MPa. However, the specific value needs to be determined according to the characteristics of the slurry and the filter press. For example, when filtering a slurry with high viscosity, a higher feed pressure may be required to overcome the resistance and achieve better filtration results.
Monitor and adjust the pressure: During the operation of the filter press, the feed pressure should be continuously monitored. If the pressure is too high, it may cause damage to the filter cloth and the filter plate, and increase energy consumption. If the pressure is too low, the filtration speed will be slow, and the filter cake may not be formed properly. Therefore, the pressure should be adjusted in a timely manner according to the actual situation.
3. Filtration Time
Determine the optimal filtration time: The filtration time is related to the nature of the slurry, the feed rate, and the desired filter cake quality. Usually, the filtration time is between 20 and 60 minutes. Shorter filtration times may result in insufficient dehydration of the filter cake, while longer filtration times may reduce production efficiency. Through experiments and production experience, the optimal filtration time for different types of slurries can be determined to achieve the best balance between filtration quality and production efficiency.
Consider the change of filtration resistance: As the filtration process progresses, the filtration resistance will gradually increase due to the deposition of solids on the filter cloth. Therefore, the filtration time should be adjusted according to the change of filtration resistance. When the filtration resistance reaches a certain value, it is necessary to stop the filtration and carry out cleaning or other operations to ensure the normal operation of the filter press.
4. Diaphragm Inflation Pressure and Time
Optimize the inflation pressure: The diaphragm inflation pressure is an important parameter for squeezing and dehydrating the filter cake. Generally, the inflation pressure is between 0.6 and 1.0 MPa. A suitable inflation pressure can effectively squeeze out the moisture in the filter cake and improve the dryness of the filter cake. However, if the inflation pressure is too high, it may cause the filter cake to crack or the diaphragm to be damaged. Therefore, the inflation pressure should be adjusted according to the characteristics of the filter cake and the equipment.
Control the inflation time: The inflation time also affects the dehydration effect of the filter cake. Usually, the inflation time is between 5 and 15 minutes. Appropriate inflation time can ensure that the diaphragm fully exerts its squeezing function and makes the filter cake reach the desired dryness. If the inflation time is too short, the dehydration of the filter cake is insufficient; if the inflation time is too long, it will affect the production cycle and efficiency.
5. Discharge Cycle
Set the discharge time: The discharge cycle should be set according to the production process and the characteristics of the filter cake. After the filtration and squeezing processes are completed, the filter cake needs to be discharged in a timely manner to start the next filtration cycle. The discharge time is usually within 5 minutes to ensure the smooth progress of the production process.
Coordinate with the feeding cycle: The discharge cycle should be coordinated with the feeding cycle to ensure the continuous operation of the filter press. By reasonably arranging the discharge and feeding times, the production efficiency can be improved, and the equipment utilization rate can be maximized.
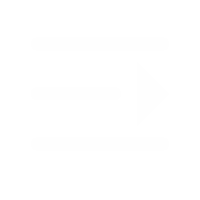
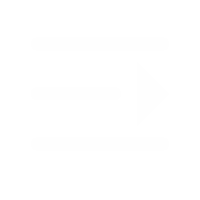
—— Contact:Manager
—— Tel:+86 16632826789
—— Email:sales@hbscfilterpress.com
—— Url:http://www.hbscfilterpress.com
—— Address:West Zone of Economic Development Zone, Fucheng County, Hengshui City, Hebei Province