NewsDetails
Analysis of Diaphragm Filter Plate Damage Reasons and the Complete Replacement and Maintenance Process
author:Shuangcheng time:2025-03-21 00:12:55 Click:85
Analysis of Diaphragm Filter Plate Damage Reasons and the Complete Replacement and Maintenance Process
I. Damage Reasons Analysis
A. Mechanical Stress - Related
Over - pressure during Filtration
Explanation: Diaphragm filter presses operate under specific pressure ranges. If the filtration pressure exceeds the design limit of the diaphragm filter plate, it can cause excessive stress. For example, in a mining application where the slurry contains a high proportion of solids, if the feed pump pressure is not properly regulated, the pressure in the filter chamber can spike. The diaphragm, which is usually made of rubber or a composite material, may stretch beyond its elastic limit. This can lead to permanent deformation, and in severe cases, rupture.
Consequence: A ruptured diaphragm will not be able to perform its function of squeezing the filter cake effectively, resulting in a wetter filter cake and reduced filtration efficiency. Additionally, the damaged diaphragm may allow solids to pass through, contaminating the filtrate.
Mechanical Impact
Explanation: During the operation of the filter press, especially during the opening and closing of the filter plates, there is a risk of mechanical impact. If the filter plates are not aligned correctly when closing, they may hit the diaphragms with force. Also, if foreign objects, such as tools or small pieces of metal, accidentally enter the filter chamber, they can scratch or puncture the diaphragm when the plates move.
Consequence: Scratches and punctures on the diaphragm create weak points. These weak points can gradually expand under pressure, leading to larger holes or tears in the diaphragm, which ultimately impairs its performance.
B. Chemical - related
Corrosion due to Slurry Chemicals
Explanation: The slurry being filtered often contains various chemical substances. In industries like the chemical industry or wastewater treatment plants, the slurry may be acidic, alkaline, or contain strong oxidizing agents. If the diaphragm material is not chemically compatible with the slurry, it will be corroded. For instance, a rubber diaphragm may be attacked by certain acids, causing it to degrade and lose its mechanical properties.
Consequence: Corroded diaphragms become brittle and less elastic. They are more likely to crack or break during normal operation, reducing the lifespan of the diaphragm and affecting the filtration process.
Chemical Degradation over Time
Explanation: Even in the absence of highly reactive chemicals in the slurry, the diaphragm material may undergo slow chemical degradation over long - term use. Exposure to air, moisture, and heat can cause oxidation and hydrolysis reactions in the diaphragm material. For example, some polymer - based diaphragms may gradually lose their strength and flexibility due to these environmental factors.
Consequence: As the diaphragm degrades, its performance deteriorates. It may not be able to withstand the normal operating pressures as effectively, leading to premature failure.
C. Wear - related
Abrasion by Solid Particles in Slurry
Explanation: When the slurry contains abrasive solid particles, such as sand or sharp - edged minerals, these particles can abrade the surface of the diaphragm during the filtration process. The continuous movement of the slurry and the pressure applied can cause the solid particles to scrape against the diaphragm, gradually wearing it down.
Consequence: Abrasion reduces the thickness of the diaphragm. As the diaphragm becomes thinner, it becomes more vulnerable to mechanical stress and is more likely to fail under normal operating conditions.
Friction with Filter Cloth and Filter Plates
Explanation: During the operation of the filter press, the diaphragm moves against the filter cloth and the filter plates. If there is improper installation of the filter cloth or if the surface of the filter plates is rough, excessive friction can occur. This friction can wear away the surface of the diaphragm over time.
Consequence: Worn - out areas on the diaphragm can lead to uneven pressure distribution during the squeezing process, resulting in an uneven filter cake and reduced filtration efficiency.
II. Replacement and Maintenance Process
A. Replacement Process
Preparation
Safety Precautions: Before starting the replacement, ensure that the filter press is completely shut down and the pressure is fully relieved. Lock out the power source to prevent accidental startup. Wear appropriate personal protective equipment, such as safety glasses, gloves, and work clothes.
Gather Tools and Replacement Parts: Collect all the necessary tools, such as wrenches, screwdrivers, and pliers. Obtain a new diaphragm filter plate of the correct model and size. Make sure the new diaphragm is in good condition and has no visible defects.
Removal of Damaged Diaphragm Filter Plate
Open the Filter Press: Carefully open the filter press to access the filter plates. Loosen the bolts or clamps that hold the filter plates together.
Identify and Remove the Damaged Plate: Locate the damaged diaphragm filter plate. Depending on the design of the filter press, you may need to remove adjacent plates to access it. Use the appropriate tools to disconnect any connections, such as hydraulic lines (if applicable) and filter cloth attachments. Lift out the damaged plate carefully.
Installation of New Diaphragm Filter Plate
Inspect the Installation Area: Before installing the new plate, thoroughly clean the area where the plate will be installed. Check for any debris, dirt, or residual slurry that could affect the installation or the performance of the new plate.
Attach the Filter Cloth: If the filter cloth is not pre - attached to the new diaphragm filter plate, carefully attach it according to the manufacturer's instructions. Make sure the filter cloth is evenly spread and properly secured.
Install the New Plate: Lower the new diaphragm filter plate into place. Align it carefully with the adjacent plates and the filter press frame. Connect any hydraulic lines or other attachments. Tighten the bolts or clamps to secure the plate in place, ensuring that the plate is firmly held but not over - tightened, as this could cause damage to the plate or the filter press frame.
Testing
Close and Pressurize the Filter Press: Close the filter press and gradually pressurize it to a low test pressure. Check for any leaks around the new diaphragm filter plate, including the connections and the edges of the plate.
Check Filtration Performance: Feed a small amount of slurry through the filter press and observe the filtration process. Check the quality of the filter cake and the clarity of the filtrate. If there are any issues, such as uneven filter cake formation or poor filtrate quality, stop the filter press and re - inspect the installation.
B. Maintenance Process
Regular Inspection
Visual Inspection: Regularly visually inspect the diaphragm filter plates during the operation of the filter press. Look for signs of damage, such as cracks, holes, bulges, or discoloration. Check the connections and the condition of the filter cloth.
Performance Monitoring: Monitor the filtration performance of the filter press. If there is a sudden decrease in filtration efficiency, an increase in the moisture content of the filter cake, or a change in the quality of the filtrate, it may indicate a problem with the diaphragm filter plate.
Cleaning
Routine Cleaning: After each filtration cycle, clean the diaphragm filter plates. Use a high - pressure water jet to remove any residual slurry on the surface of the plate and the diaphragm. Avoid using harsh chemicals that could damage the diaphragm material.
Deep Cleaning: Periodically, perform a deep cleaning of the filter plates. This may involve soaking the plates in a suitable cleaning solution (if compatible with the diaphragm material) to remove stubborn deposits.
Lubrication (if applicable)
Moving Parts: If the filter press has moving parts related to the diaphragm, such as hydraulic cylinders or mechanical linkages, lubricate these parts regularly. Use the appropriate lubricant recommended by the manufacturer to reduce friction and wear.
By understanding the common damage reasons and following the proper replacement and maintenance procedures, the lifespan of diaphragm filter plates can be extended, and the efficient operation of the diaphragm filter press can be ensured.
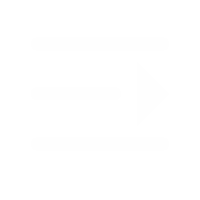
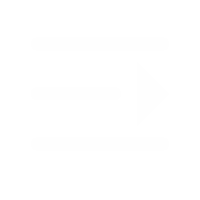
—— Contact:Manager
—— Tel:+86 16632826789
—— Email:sales@hbscfilterpress.com
—— Url:http://www.hbscfilterpress.com
—— Address:West Zone of Economic Development Zone, Fucheng County, Hengshui City, Hebei Province