NewsDetails
Master These Tips, Easily Solve Common Faults of Diaphragm Filter Press Plates
author:Shuangcheng time:2025-04-28 00:03:11 Click:80
In the process of industrial solid-liquid separation, the diaphragm filter press has become a powerful assistant for many enterprises due to its efficient filtration performance. However, as the core component, the filter plate can directly affect the operational efficiency and production schedule of the filter press when it malfunctions. Understanding the common faults of diaphragm filter press plates and mastering scientific and effective solutions are of great significance for ensuring the continuity of industrial production and reducing maintenance costs. This article will systematically sort out common faults and coping strategies of filter plates to help you easily address equipment issues.
I. Basic Understanding of Diaphragm Filter Press Plates
1.1 Definition and Structure
The diaphragm filter press plate is a key component for achieving solid-liquid separation, primarily consisting of a filter plate body, an elastic diaphragm layer, a feed inlet, and a filtrate outlet. The filter plate body provides structural support, while the diaphragm layer is responsible for pressing and dewatering. The feed inlet and filtrate outlet handle material introduction and filtrate discharge, respectively. All parts work closely together to complete efficient filtration.
1.2 Working Principle
During operation, material enters the filter chamber formed by the filter plate and filter cloth through the feed inlet. Under pressure, liquid passes through the filter cloth and is discharged through the filtrate outlet, while solid particles are retained to form a filter cake. In the later stage of filtration, the diaphragm layer is inflated with gas or liquid to press the filter cake, further reducing its moisture content and achieving efficient solid-liquid separation. Understanding the structure and principle of the filter plate is the basis for accurately diagnosing and solving faults.
II. Common Faults and Cause Analysis of Diaphragm Filter Press Plates
2.1 Leakage Between Filter Plates
Leakage between filter plates is one of the common faults. The main causes include wear on the sealing surface of the filter plate, aging or damage of the sealing gasket, folding or damage of the filter cloth, and misalignment of the filter plates. The sealing surface is prone to scratches due to prolonged friction with the material, leading to poor sealing. The sealing gasket gradually loses its elasticity under frequent pressing and chemical erosion. Abnormal conditions of the filter cloth can also disrupt the sealing effect.
2.2 Slow Filtration Speed
A significant decrease in filtration speed can affect production efficiency. Multiple factors contribute to this issue, such as blocked filter cloth, insufficient feed pressure, blocked filter plates, and damaged diaphragm layers. Prolonged use of the filter cloth can clog its pores, impeding liquid passage. Unstable or insufficient feed pressure cannot push the material through quickly. Blocked internal channels of the filter plate due to dried material can also reduce filtration speed.
2.3 Damage or Deformation of Filter Plates
Damage, cracks, or deformation of filter plates not only affect filtration efficiency but may also pose safety hazards. Overpressure operation is a common cause of filter plate damage. Excessive pressure beyond the filter plate's tolerance can cause cracks or even rupture. Additionally, poor filter plate material quality, long-term exposure to corrosive materials, and improper stacking of filter plates can also accelerate damage.
2.4 Diaphragm Layer Malfunction
Diaphragm layer malfunctions primarily manifest as bulging, damage, or poor pressing effect. Long-term use may cause damage due to material aging, uneven internal pressure, or punctures from sharp objects. A damaged diaphragm layer cannot effectively press the filter cake, reducing the dewatering effect and impacting solid-liquid separation quality.
III. Solutions to Common Faults of Diaphragm Filter Press Plates
3.1 Addressing Leakage Between Filter Plates
To address leakage between filter plates, first inspect the sealing surface. If there is minor wear, use sandpaper to smooth it out. Replace aged or damaged sealing gaskets promptly. Readjust the filter cloth position to ensure it is flat and unfolded, and replace any damaged cloth. Additionally, check if the filter plates are fully aligned and make fine adjustments to tightly fit them together, restoring sealing performance.
3.2 Improving Filtration Speed
When filtration speed slows down, start by cleaning or replacing the filter cloth to remove impurities blocking its pores. Inspect the feed pressure system and ensure the pressure is stable within a reasonable range, adjusting it if necessary. If the filter plate is blocked, disassemble it to clean dried material from the internal channels. For filtration speed issues caused by a damaged diaphragm layer, replace it with a new one.
3.3 Repairing or Replacing Damaged Filter Plates
Upon discovering damage or deformation of the filter plate, if the damage is minor, use welding or repair agents for repair. However, for severely damaged or deformed filter plates, ensure equipment safety and filtration effect by promptly replacing them. When replacing filter plates, choose models and materials that match the original equipment to ensure correct installation.
3.4 Resolving Diaphragm Layer Malfunctions
When the diaphragm layer shows bulging, damage, or other issues, disassemble the filter plate to inspect the damage. Minor damage can be repaired using specialized repair materials, while severe damage requires replacing the diaphragm layer. When installing a new diaphragm layer, ensure no air is trapped inside to maintain normal pressing effect.
IV. Measures to Prevent Faults of Diaphragm Filter Press Plates
4.1 Standardizing Operation Procedures
Operators should strictly follow equipment operating procedures to avoid faults caused by improper operation. Follow the correct sequence during equipment startup and shutdown. Control the filtration pressure within the specified range to prevent overpressure operation. Clean residual material from the filter plate surface promptly to avoid damage from dried material.
4.2 Strengthening Routine Maintenance
Establish a comprehensive routine maintenance system to regularly inspect the condition of filter plates, filter cloth, sealing gaskets, and other components. Clean the filter plate surface and chamber promptly to keep the equipment clean. Lubricate and maintain moving parts of the filter plate to ensure smooth operation. Regularly inspect critical components such as the pressure system and feed system and address any abnormalities promptly.
4.3 Reasonably Selecting and Using Filter Plates
Choose filter plates with appropriate materials and specifications based on material properties and working environments. For highly corrosive materials, select filter plates with good corrosion resistance. In high-temperature environments, choose heat-resistant filter plates. Additionally, avoid overloading the filter plates and reasonably arrange equipment operating hours to extend their service life.
V. Conclusion
Common faults are inevitable during the use of diaphragm filter press plates. However, by deeply understanding the structure and working principle of the filter plate, accurately diagnosing fault causes, adopting scientific and effective solutions, and implementing routine preventive measures, one can easily address common faults. By standardizing operations, strengthening maintenance, and reasonably selecting filter plates, not only can the stable operation of the diaphragm filter press be ensured, production efficiency can be improved, and equipment maintenance costs can be reduced, providing strong support for the continuous and efficient operation of industrial production.
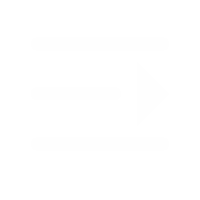
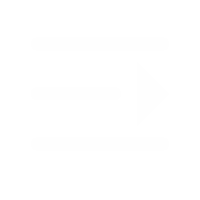
—— Contact:Manager
—— Tel:+86 16632826789
—— Email:sales@hbscfilterpress.com
—— Url:http://www.hbscfilterpress.com
—— Address:West Zone of Economic Development Zone, Fucheng County, Hengshui City, Hebei Province